As a Financial Accountant, I have witnessed a significant shift in my approach to Supply Chain Management (SCM) over the past two years. The integration of SCM and Project Management & Accounting (PMA) on Microsoft Dynamics 365 has been transformative.
Lately, my focus has been on implementing PMA and delving into Master Requirement Planning (MRP) discussions daily, particularly within the Manufacturing/Production & Assembly Plants.
When it comes to client requirements, there are two distinct strategies to consider:
– Manufacturing an item and incorporating it into the Project, where inventory is expensed against the Project. This method ensures that items produced are not available for other uses, making it ideal for specific customer orders or capitalizing on items post-production.
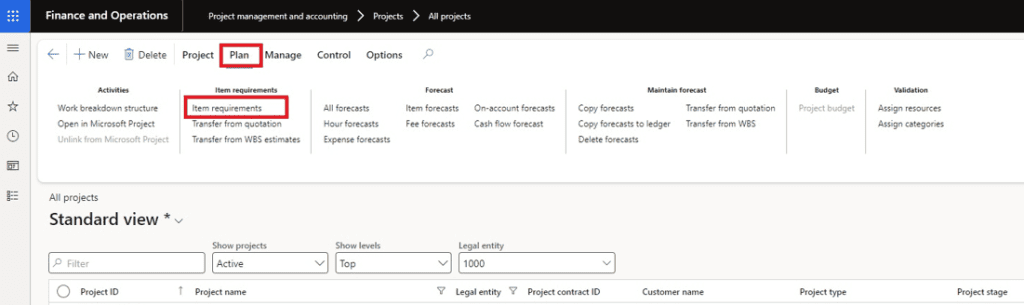
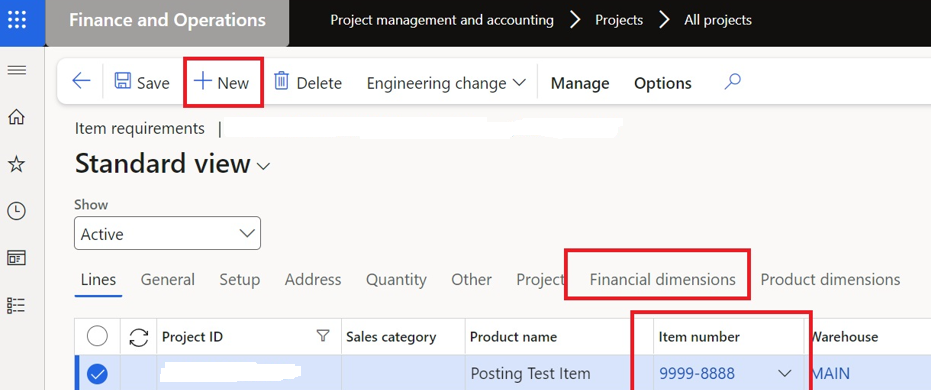
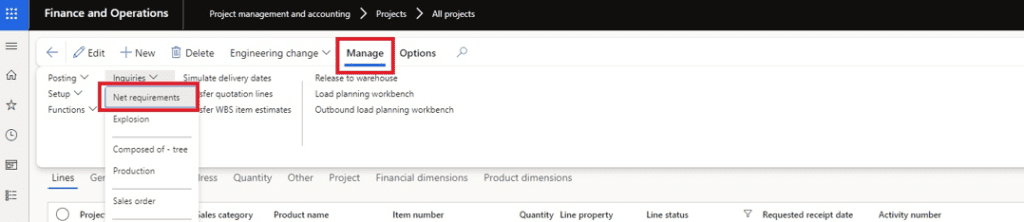
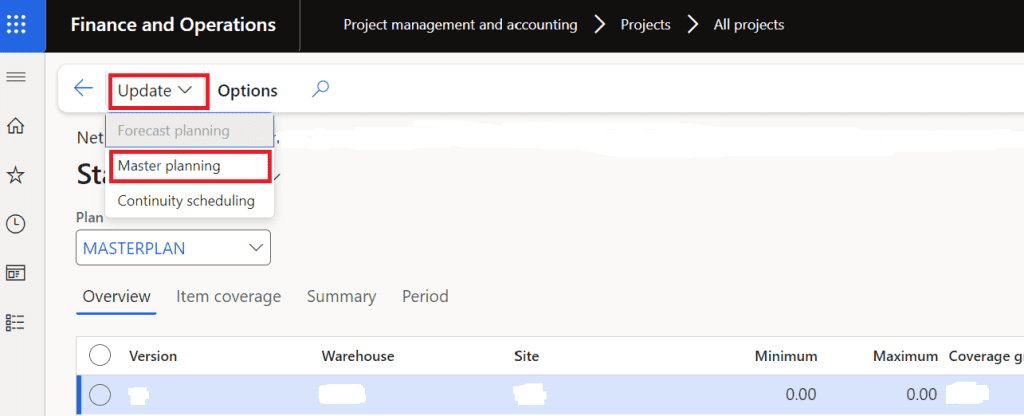
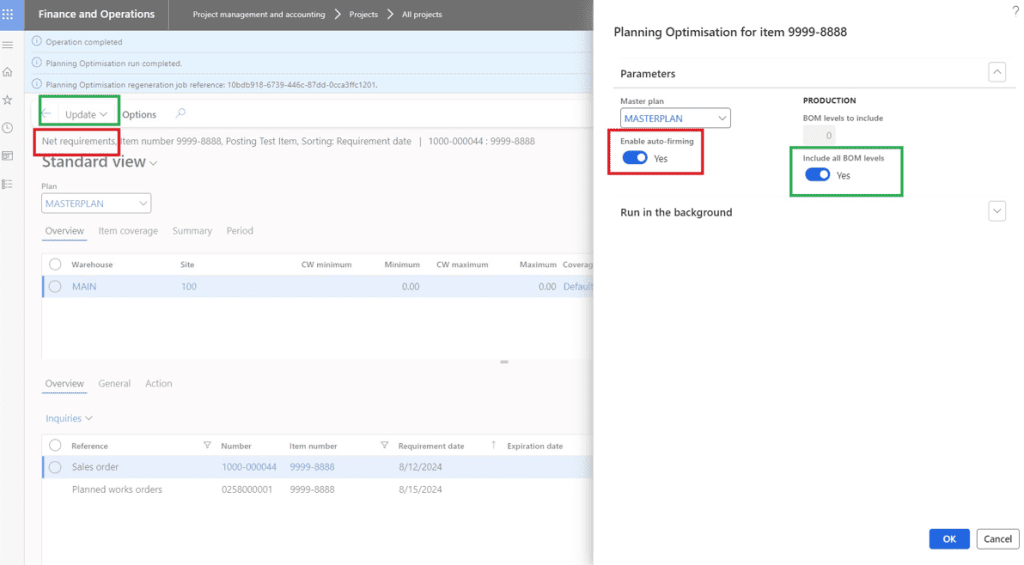
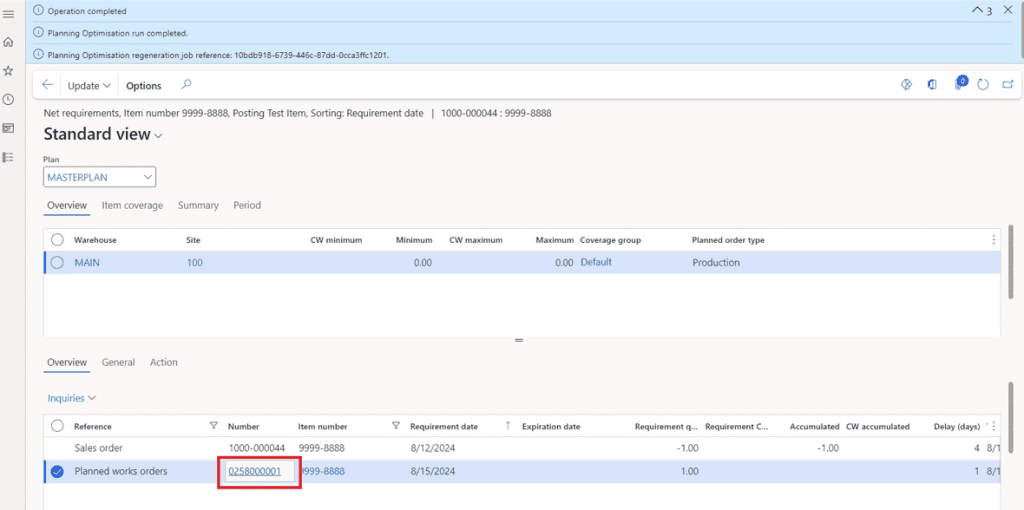
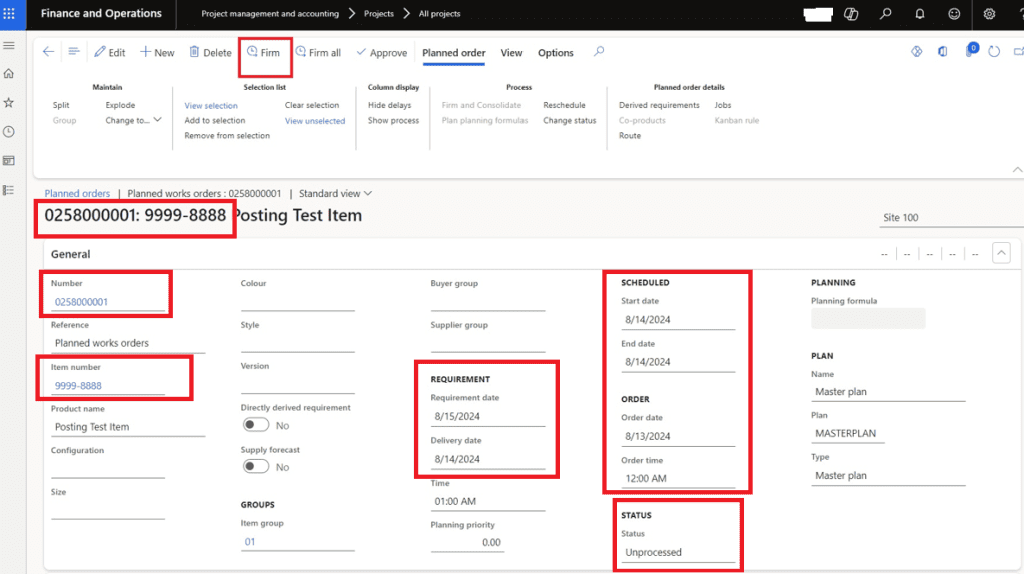
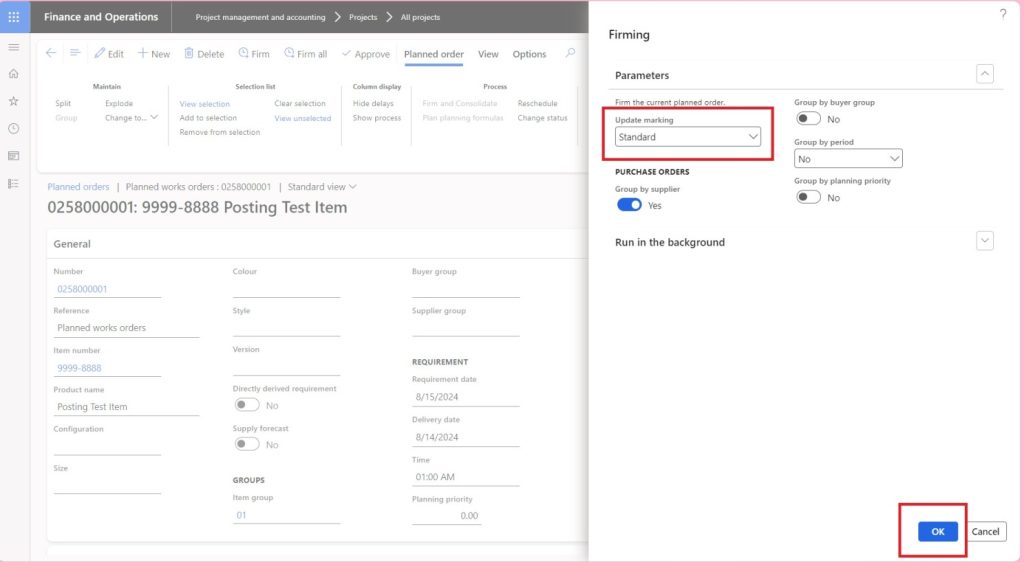
Manufacture items for a specific Campaign/Product Line and track everything against that Campaign/Product Line as a Project but leave the item in stock when production ends.
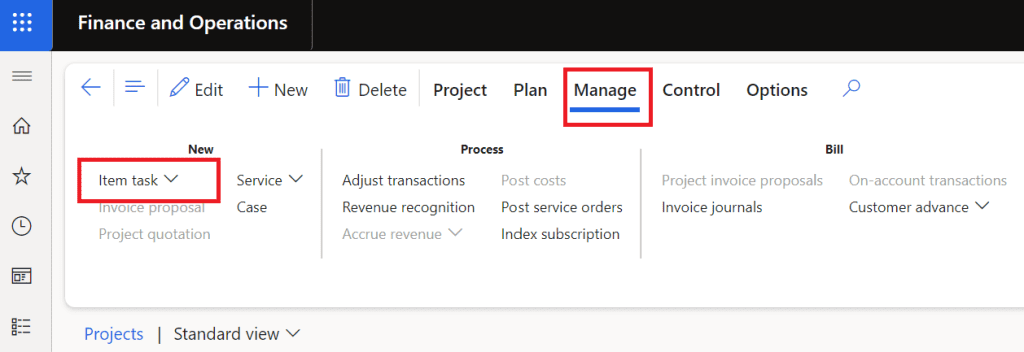
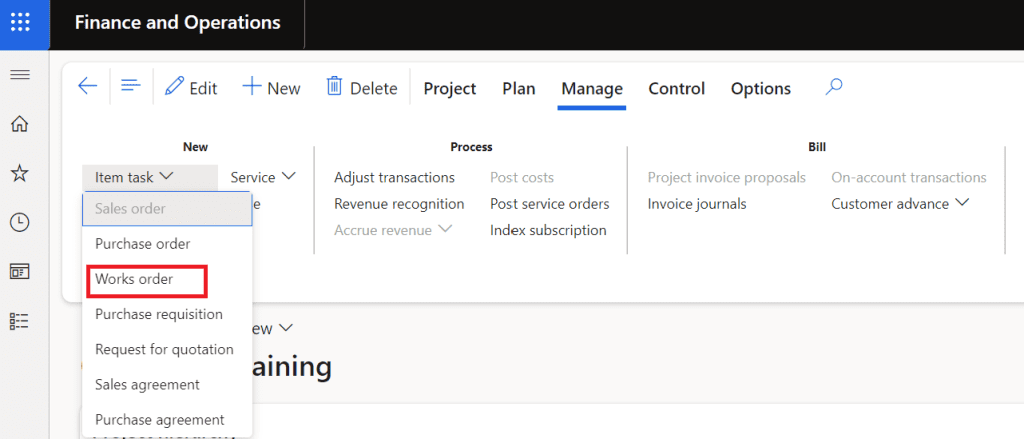
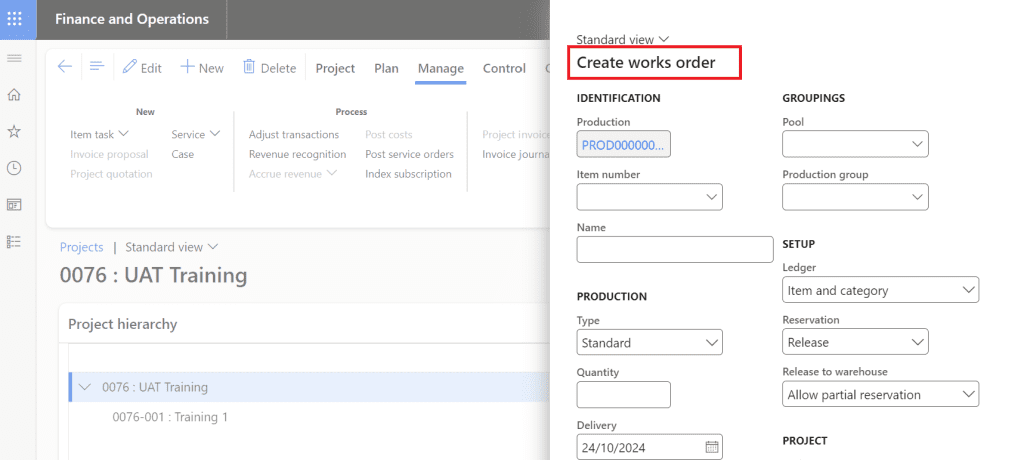
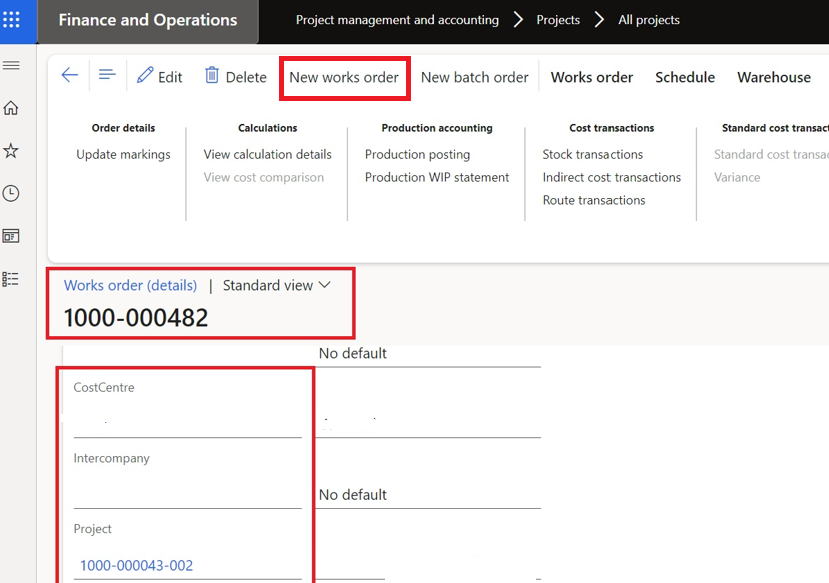

If you are considering migrating your ERP to Microsoft Dynamics 365 or Business Central for your Production/Manufacturing process, reach out to us at support@mosoftwares.com or schedule a call via our website www.mosoftwares.com to discuss how we can assist you.